Trenitalia improves rolling stock maintenance using big data
Posted: 25 July 2016 | Danilo Gismondi | No comments yet
Rolling stock maintenance is an expensive and critical process for a railway company. Trenitalia has managed to make it more effective by using a dynamic maintenance system which combines the Internet of Things (IoT) with analytics and in-memory computing. For Global Railway Review, Trenitalia’s CIO, Danilo Gismondi, shares the details of these all-encompassing technologies and how they are working to keep Italy’s rolling stock on track…
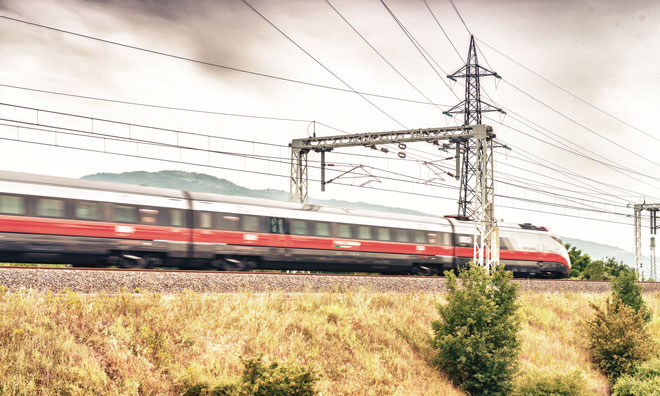
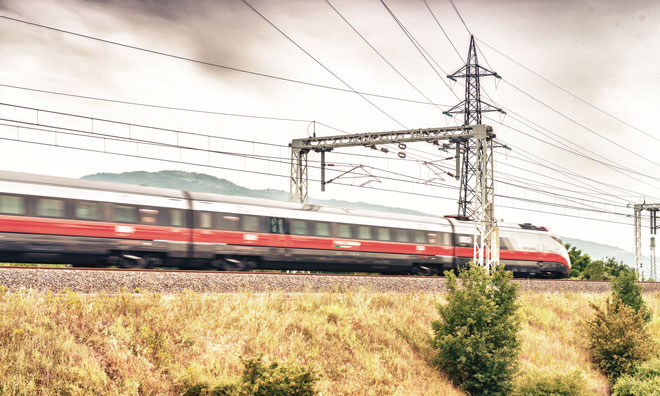
Big data is transforming our understanding of everything from fetal development to cosmology. Scientists have found that toddlers learn language not from repetition – which has been believed for centuries – but by hearing words used in multiple contexts. Epidemiologists, using Google search data, can now spot an emerging epidemic before doctors do. The commercial impact of this technology can be found everywhere, from products and services that can predict the unique needs of individual customers, to stores that adapt – via means of special discounts and deals that pop up on smartphones – to each customer who walks through the door.
But how has the railway industry benefited from this revolution?
One of the most expensive and critical processes for a railway company is rolling stock maintenance.
Trenitalia has managed to improve it by analysing data coming from thousands of sensors installed aboard trains. The Dynamic Management Maintenance System (DMMS), built on a Sap Hana platform, can predict failures before they actually happen.
A paradigm shift
This innovative method, termed Condition Monitoring, involves monitoring the operation of some components and performing only necessary maintenance activities, thus minimising overall costs – which can be reduced by up to 8%.
Traditionally, rolling stock maintenance has been carried out with two kinds of approaches: one corrective and another preventive.
The first relies on specific maintenance activities that are performed only when an anomaly or a component failure is occurring or has occurred. These failures are identified thanks to a diagnostic platform, whose functioning is dependent on specific sensors installed on trains, along with several on-earth control units that gather and analyse data.
The second approach consists of quite long and expensive activities carried out on the train, which usually imply maintenance cycles scheduled on variables such as kilometre-based thresholds. The problem with relying on this approach is that these variables do not precisely represent the real health condition of each component, which in reality is more related to its different uses: the manner of service offered by the vehicle; number of journeys per day; the hardness of average rides; and relevant environmental conditions and crowding levels.
However, recent advances in sensor and communication technologies have enabled constant data collection from various systems in trains – meaning that mechanical and electrical conditions, operational efficiency and other performance indicators can be monitored 24 hours a day. The data stored in the Sap Hana platform are then searched with predictive algorithms. If patterns that indicate potential failures are found, then the actual maintenance process is activated.
Knowing when to replace a component
The pantograph is a case in point. An algorithm searches for behaviours of the pantograph that deviate from the norm, using recordings of the lifting time. If inconsistencies are detected a technician will receive a text message, meaning that a maintenance alert will be opened and the replacement organised before any failure can occur.
The implementation of such an innovative system, however, implies the presence of a capillary diagnostic system that includes a myriad of sensors placed on trains, as well as control units that are able to channel this information to the system to then be utilised for health condition analysis.
Sap Hana, the platform on which Trenitalia’s system is built, integrates different layers: the in-memory computing enabling real or near real-time processing; the database and the analytics. It allows Trenitalia to handle huge volumes of data in a time-responsive manner.
This innovative system allows maintenance to be carried out when a component is about to break, thus minimising the number and cost of unscheduled circulation interruptions caused by actual failures. In addition, it can ensure that repaired equipment is in an acceptable condition as most mechanical problems can be reduced if they are detected and repaired early.
Condition monitoring will lead to cost savings
This innovative big data system will lead to cost savings in at least three areas: the number of interventions; duration of each intervention; and number of substituted pieces.
The first case may appear counterintuitive as the number of times the train is in maintenance plan will increase due to the controls for a single component. However, the number of performed interventions will significantly decrease thanks to the possibility of avoiding useless controls.
The duration of each maintenance activity will also be faster thanks to both the installation of high technological devices able to rapidly spot anomalies in a component’s condition, and the greater confidence in solving problems given by the definition of parts’ expected life patterns and fault probabilities.
The number of substituted pieces will be reduced as well. Each component will be replaced only when it actually needs to be, rather than merely relying on pre-determined standards, which often lead to unnecessary replacements. Stock amount will also decline as the predictive model will enable teams to schedule purchasing requirements in advance, allowing the time that spare parts are kept in stock to be reduced.
Last but not least, the quality of suppliers will be improved with the constant and thoughtful monitoring of components which enable the building of statistics about components’ performances, which indirectly implies an assessment of a supplier’s delivered quality.
Rolling Stock Maintenance goes digital
The DMMS has given rise to another initiative aimed at making the whole maintenance activity completely digitalised. It implies a real change in the way these activities are performed and is a requirement in order for the whole project to succeed.
The basic idea is that of providing maintenance engineers with tablets whose primary goal, at least in the initial step, is gathering feedback about components, when checked or substituted, which is then sent and used by the DMMS system for indicators and thresholds adjustments. Upon completion of the initiative, the technological devices provided to maintenance engineers will enable them to perform tasks such as work order settlements and checking the availability of spare parts.
Also, they will be provided with access to a social network platform to share doubts and uncertainties regarding faults and detected issues with other maintainers all over the world.
A maintenance revolution is coming
In summary, the DMMS is going to bring a deep-routed change, not only in the way maintenance is approached – switching from a corrective/preventive system to a predictive one – but also in the way maintenance activities are performed, enabling a purely digital transformation of all the main activities. Maintenance digitalisation will be achieved through the implementation of concrete tools to detect faults, such as scanners and robots, along with the introduction of tablet devices to manage the whole maintenance pattern.
Another important element of innovation is the switch from the current situation of scarce communication between different partners and actors involved in the transportation delivery service (suppliers, maintainers, engineers, technicians, external partners) to that of a completely integrated system. In this way, all actors are able to communicate between themselves and share information taking advantage of each other’s skills and capabilities.